B.A. Sunderlin Bellfoundry is one of only three of its kind left in the United States.
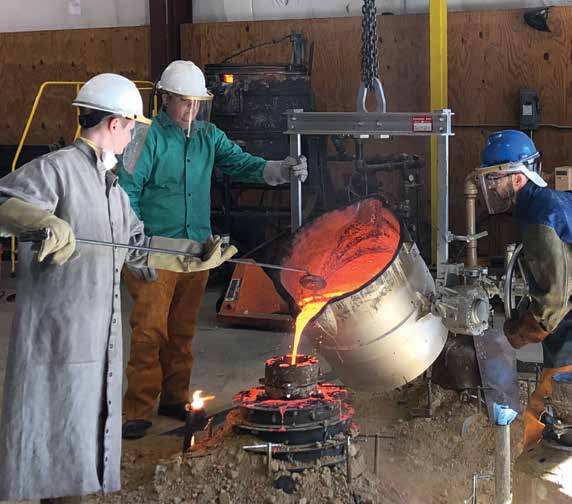
Pouring heated bronze into a mold that will become a bell.
Bells have played an important role in communities, churches, and schools for centuries by marking the hours, inviting to prayer, and commemorating important occasions. To this day, their majestic ringing echoes through cities and towns across the world. But nearly all of the foundries that manufacture them have long disappeared.
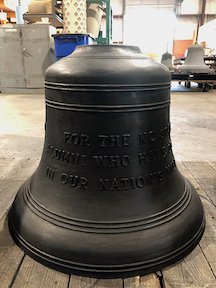
Finished bell bound for North Carolina State University.
In the United States, foundries began casting bells as early as 1717, when John Philips of New York City was the first founder to call attention to this craft. In the following decades, foundries spread through Massachusetts, Vermont, Pennsylvania, and Maryland, and then to the Midwest, from Cincinnati to St. Louis. Today, however, only three remain in the country—and one of them is here in Virginia.
B.A. Sunderlin Bellfoundry in Ruther Glen has been in business since 2015, casting 50 to 75 bells each year. “We have been very fortunate to be able to have enough work to rebuild this industry a little bit,” says Benjamin Sunderlin, a bellmaker and campanologist, who runs the foundry with his wife, Kate. Campanology is the study of bells: how they are cast, tuned, rung, and sounded, as well as the history, methods, and traditions of bell ringing as an art.
The couple met in 2012 at the University of Notre Dame, where they were pursuing Master’s degrees in studio art and art history, respectively. “As our relationship started to get more serious, we started to envision how we might marry our interests and goals,” says Kate. Ben had been working in the bell industry for a few years at that point and knew that he wanted to open his own foundry someday. When Kate was accepted into a PhD program at Virginia Commonwealth University, the couple moved to Port Royal, and Ben opened his business in Ruther Glen: a full-service nonferrous foundry that focuses on cast bronze bells and includes a museum-like space to discuss the art and science of campanology, where they also offer tours for visitors.
In the five years since the foundry’s opening, it has grown to 12 employees. The couple’s biggest project to date—which they are currently working on—is making a 55-bell carillon for North Carolina State University. The foundry also services and maintains instruments throughout the United States and undertakes restoration work, such as a project completed recently for the Leaning Tower in Niles, Illinois. “An early project in this vein was creating a bell based on found bell fragments for Historic Jamestowne,” Kate says.
Like bronze statues, bells can be made in several different ways. The Continental Method relies on a swept-loam molding technique (loam is a mixture of sand, hair, horse dung, and clay, and it helps shape the mold). The English Method uses cast-iron flasks (bell shaped cases) lined with loam; one part of the flask functions as the core and the other as the cope, or top. The Sunderlins are the only bell foundry in the country that uses both methods.
Foundry work is inherently stressful. Workers labor over a mold for days or weeks, meticulously seeing to every detail. “Then, when the mold is poured, all of your work is put to the test when 2,000-degree molten bronze flows into the cavity,” Kate says. “You exchange hours of labor in molding for two minutes of sheer anxiety when the bell is cast.” If there’s even a tiny flaw in the surface of the casting, the bell must be remade. “All of the work is for naught. This happens very rarely, but when we are testing a new profile, it could happen,” Kate says. The metal, however, is always recycled. Old bells are also broken up and remelted; even the chips that are cut out of the bells will be remelted and used again.
The process of tuning is an art itself. Bells produce multiple notes that need to be tuned relative to each other by cutting metal from different places inside the bell. One cut doesn’t just tune one frequency, but affects others as well. If the tuner removes too much metal and a note goes too flat, then the bell may also need to be remade. “Again, this is very rare,” says Kate, “but if the tuner doesn’t pay close attention to their work, it can all be ruined at the end of the program.” Fortunately, she adds, “Bells don’t fall out of tune once they are tuned. In this respect, this process is more like diamond cutting instead of tuning something like a guitar.”
Part of what makes the craft challenging is that there is no school for bellfounding. Ben had to seek the knowledge from other masters, while also experimenting to craft a profile unique to his foundry. “People generally know very little of bellfounding, and so there is a bit of a learning curve in terms of explaining to people what this science is and why it matters,” Kate says.
The same goes, naturally, for the foundry’s staff, who are dedicated to their work. “One of the things I love most about working at the foundry is that, in addition to preserving a historic craft, I get to look forward and use modern technology to better understand how and why people have been making bells this way for centuries, as well as apply that technology to make the tradition more accessible to future generations,” says Thomas Sheehan, the foundry’s technician, designer, and draftsman.
Although many bell foundries are going out of business—one in the United Kingdom closed after 450 years, and another in the Netherlands after 360 years—the Sunderlins are optimistic about their foundry’s future. “While we mourn the passing of these foundries and celebrate their extremely long tenure in making bells, we are also incredibly galvanized to save a craft from extinction here in North America,” Ben says.