Twenty years ago, Sara McCaleb Baldwin started making classical motif mosaics. Today, New Ravenna Mosaics produces a luxury product sought by America’s top architects and interior designers.
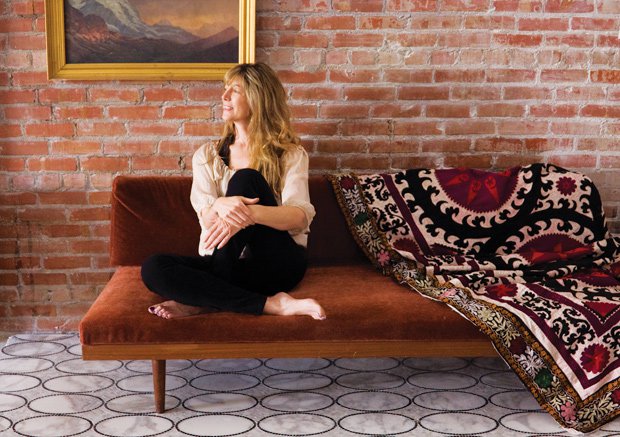
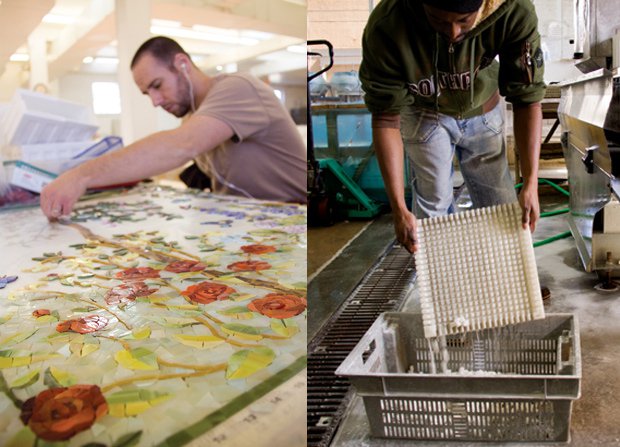
Left: Mosaicist Bobby Jones works on a wall mural; right, a square foot of tesserae.
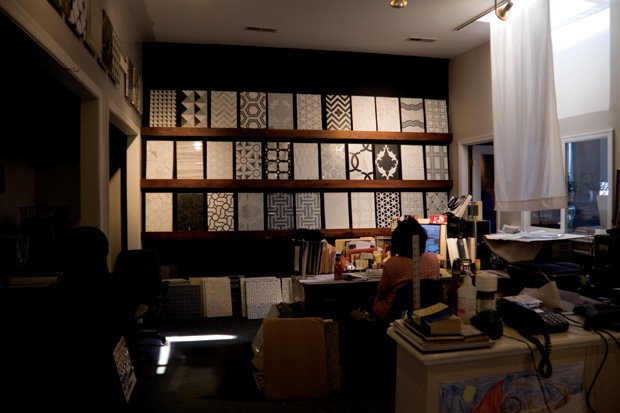
A sampling of New Ravenna’s private-label designs.
Sitting in a light-drenched Eastern Shore warehouse building, with heavy metal music coursing through his headset, Bobby Jones concentrates on the task in front of him: assembling a three-by-three-foot wall mural with an English garden motif. The design is complicated, and bringing it to life requires a painter’s awareness of color and shading and a lapidarist’s touch to fit the small tiles, called tesserae, into place. Jones, a self-taught artist and virtuoso mosaicist for New Ravenna Mosaics, rummages through boxes of stained glass until he finds the perfect hue of blue violet tessera needed for a delphinium. From start to finish, it will take Jones about a week to finish the mosaic, which then will be shipped off to Seattle, there to adorn a client’s bathroom wall.
About 20 steps past Jones’ work table, Sara McCaleb Baldwin, the founder and owner of New Ravenna Mosaics, huddles with her design staff. The group is scrutinizing a preliminary drawing for a large mural that a financial center in Dubai wants to install in its office. The potential purchaser’s interior design firm has supplied a rough sketch, and New Ravenna and two competitors, located in Italy and Canada respectively, are competing for the job. Cean Irminger, a nine-year New Ravenna employee, is creating the design, and she wants her colleagues’ input. Baldwin is happy to oblige. Big projects like this one are not as common as they were before the economic downturn, and so she and the designers want to win the contract. Playing the role of both editor and cheerleader at the small conclave, Baldwin makes concrete design suggestions that seem to energize the group.
Competing with Italian mosaic factories is just another surprising chapter in the unlikely story of New Ravenna, a company that produces a highly refined luxury product amid the easygoing environs of rural Northampton County. The 20-year-old firm is a few thousand miles and many centuries removed from its artistic antecedents in classical Greece and Rome. However, time and distance haven’t changed the nature of the business. Making mosaics remains a labor-intensive craft that often soars to the level of art—and when that happens consistently, orders follow. Today, New Ravenna mosaics are sold through nearly 200 independent design showrooms across the country, including nine in Virginia, plus a growing number outside North America.
The company’s client list is a who’s-who of top architects and interior designers, including Robert A.M. Stern, Bunny Williams and Jamie Drake, and, according to company officials, celebrities such as Tom Hanks, Madonna, John Travolta and Tommy Hilfiger have custom-designed New Ravenna mosaics in their homes. Baldwin, inclusive by nature, emphasizes that success has been a group effort. “Every custom piece represents the shared creativity of the designer, the client, the showroom and us,” she says. “We all have a hand in it.”
Baldwin, who grew up on a farm near Craddockville in Accomack County, made her first mosaic when she was in graduate school at the University of Pennsylvania. It was her thesis project for a master’s degree in fine art. Although trained as a painter at Penn (where she earned her undergraduate degree), Baldwin discovered an unexpected passion for classical mosaics when, in 1989, she was taken with a Roman floor on exhibit at New York’s Metropolitan Museum of Art. Long drawn to functional art, Baldwin was inspired to create prototypes for a line of mosaics based on classical designs. She named her company New Ravenna in homage to Ravenna, the Italian town renowned for the mosaics in its Byzantine era churches. Baldwin lugged heavy sample boards to big-city showrooms and interior design studios. Many of those early contacts immediately recognized the decorative possibilities of an all-but-forgotten art form.
Although New Ravenna began as a cottage business, it soon outgrew its space. Baldwin then moved to a rented storefront on Highway 13, and outgrew that building, too. Today, the firm is spread among four buildings, including a former shirt factory and an old movie theater, in the little town of Exmore. The warehouse, located in the movie theater, holds a million-dollar inventory of marble and colored stones imported from Europe, the Middle East, Asia and South America. Much of it comes in 12-by-12-inch squares that are cut on-site into tesserae, the small one-half-inch square tiles used in mosaics. New Ravenna also imports larger stone tiles to give customers an exact match for the mosaic colors. A neighboring building has a huge stock of stained glass from a couple of premier American manufacturers. Jeride Beach, a former supply specialist in the U.S. Army, manages the inventory, delivering what the mosaicists need to the factory floor.
Three years ago, with the company in a growth phase, Baldwin hired Wes LaBlanc, a Philadelphia-based management consultant and longtime friend, as president of the company. He oversees the operation and conceives strategic objectives, commuting to Exmore three days a week. His arrival freed Baldwin to concentrate on her first love. “My heart is really in the artistic side of the business,” she explains. “I can manage the business side but find it freeing to be able to concentrate on design and product development.”
These days, private-label work is a lucrative and growing part of New Ravenna’s business. The company creates exclusive designs for Walker Zanger, Waterworks, Kohler Surfaces and Ann Sacks. Baldwin and her design team welcome the challenge of custom work. They begin by translating the architect’s or interior designer’s sketch into a line drawing, then into a scale drawing. Two of the team are whizzes at computer-assisted design. With client approval of the scale drawing, mosaicists create a full-scale sample. Once that is approved, the project goes into production. Because of the factory’s layout, Baldwin and the other designers walk through the second-floor production area daily on their way to and from the design studio. They are readily available to tweak the design, if necessary, and help solve problems.
Thomas Hickey, a New York architect and founding partner of GRADE Architecture and Interior Design, first met Baldwin eight years ago when he was at Robert A.M. Stern Architects. “Our clients specifically wanted mosaics from New Ravenna, but Robert Stern was very particular about what gets included in his houses,” says Hickey. “So I visited the factory in Exmore and was thoroughly impressed. Since then, I’ve worked with New Ravenna to develop custom-design mosaics for each of our projects.”
Not everyone can make mosaics. Potential hires take a skill test to see if they are good candidates for the work. According to Baldwin, one needs spatial intelligence, good color sense and manual dexterity to master the craft. One also has to have hand strength to nip stone or glass tiles into the right shapes. Some mosaicists are art school graduates, but backgrounds vary considerably. Some New Ravenna employees previously held jobs in health care, agriculture, education and retail.
Jodie Sokol, one of New Ravenna’s first mosaicists and now the director of manufacturing and warehouses, puts each new employee under the tutelage of an experienced mosaicist and then observes. “Within the first month, we can tell if new hires are going to develop into mosaicists,” she says. “Those with art ability excel.” Mosaicists are paid for what they produce, according to human resources director Mary Harris. “Workers learn through experience the techniques that enable them to make good wages plus benefits.”
While Bobby Jones and other mosaicists on the second floor work on complicated custom designs, workers on the first floor make the borders and backgrounds shown in New Ravenna catalogs. According to Kendall Harmon, a former restaurant cook who is the mosaic production manager, five quality control people check each piece before it’s shipped out. “We’re looking to see if the colors are consistent, that every piece fits and there are no chipped or cracked tiles,” he says.
Baldwin says that her designs have evolved over time, and that lately nature has been an inspiration. Bamboo, feathers, leaves and wave patterns are featured in the Metamorphosis Collection that New Ravenna offers under the name Sara Baldwin Design. “I’ve always been fascinated with pattern,” says the owner, “but now I’m exploring texture to add a three-dimensional quality to a normally flat medium. Whether it involves grinding the polish off the tiles to make them matte or tumbling the tesserae to soften the edges, texture can make mosaics more interesting and enticing.”
Tom Savage, director of Winterthur, a premier decorative arts museum based in Henry Francis du Pont’s former estate in Delaware, applauds Baldwin’s commitment and success. “The art of mosaic is just as relevant for today’s living as it was in ancient Pompeii,” he says. “Sara has simultaneously revived an ancient craft and a rural community.”
And what are Baldwin’s goals? “I’d like to grow revenues but not the size of the company. When I started this, I had no idea how it would evolve. I just wanted to make a living and create a company where I would like to work.” Over the last couple of years, she’s come to appreciate the power of synergy and artistic collaboration. “Under the best circumstances, two plus two can equal more than four.”